The Scientific Research Behind Porosity: A Comprehensive Overview for Welders and Fabricators
Comprehending the intricate systems behind porosity in welding is vital for welders and makers pursuing flawless craftsmanship. As metalworkers delve into the depths of this phenomenon, they discover a world governed by numerous aspects that affect the formation of these small voids within welds. From the composition of the base materials to the details of the welding process itself, a wide variety of variables conspire to either aggravate or relieve the visibility of porosity. In this extensive overview, we will certainly unwind the science behind porosity, discovering its impacts on weld top quality and unveiling advanced strategies for its control. Join us on this trip through the microcosm of welding imperfections, where precision satisfies understanding in the pursuit of flawless welds.
Understanding Porosity in Welding
FIRST SENTENCE:
Exam of porosity in welding exposes critical understandings into the honesty and high quality of the weld joint. Porosity, defined by the existence of dental caries or voids within the weld metal, is a typical worry in welding processes. These gaps, if not effectively addressed, can endanger the architectural honesty and mechanical residential properties of the weld, leading to potential failings in the finished item.

To identify and measure porosity, non-destructive screening methods such as ultrasonic testing or X-ray assessment are typically utilized. These methods enable for the identification of inner flaws without jeopardizing the honesty of the weld. By analyzing the dimension, shape, and circulation of porosity within a weld, welders can make enlightened decisions to improve their welding processes and attain sounder weld joints.

Variables Influencing Porosity Development
The event of porosity in welding is affected by a myriad of factors, varying from gas securing efficiency to the ins and outs of welding specification setups. One essential factor adding to porosity development is inadequate gas shielding. When the securing gas, usually argon or CO2, is not efficiently covering the weld pool, atmospheric gases like oxygen and nitrogen can pollute the liquified steel, resulting in porosity. Furthermore, the cleanliness of the base materials plays a significant duty. Impurities such as rust, oil, or moisture can vaporize during welding, creating gas pockets within the weld. Welding criteria, including voltage, current, travel speed, and electrode kind, likewise influence porosity formation. Utilizing incorrect settings can generate excessive spatter or warmth input, which subsequently can cause porosity. The welding technique used, such as gas steel arc welding (GMAW) or protected steel arc welding (SMAW), can influence porosity development due to variations in warm distribution and gas protection. Understanding and controlling these variables are important for lessening porosity in welding procedures.
Effects of Porosity on Weld Quality
Porosity development considerably endangers the structural honesty and mechanical homes of bonded joints. When porosity is present in a weld, it creates spaces or tooth cavities within the material, minimizing the overall stamina this content of the joint. These gaps serve as anxiety concentration factors, making the weld extra vulnerable to fracturing and failure under load. The visibility of porosity additionally deteriorates the weld's resistance to rust, as the caught air or gases within deep spaces can react with the surrounding atmosphere, why not try these out leading to deterioration gradually. In addition, porosity can prevent the weld's ability to withstand stress or influence, more threatening the general top quality and reliability of the welded structure. In crucial applications such as aerospace, automobile, or structural buildings, where security and sturdiness are extremely important, the damaging results of porosity on weld quality can have serious repercussions, emphasizing the importance of minimizing porosity via correct welding techniques and procedures.
Methods to Reduce Porosity
Additionally, using the suitable welding criteria, such as the proper voltage, present, and take a trip rate, is vital in stopping porosity. Preserving a regular arc size and angle during welding likewise helps minimize the chance of porosity.

Furthermore, choosing the right protecting gas and keeping proper gas circulation prices are essential in minimizing porosity. Using the proper welding strategy, such as back-stepping or utilizing a weaving motion, can also assist distribute warm equally and decrease the possibilities of porosity development. Last but not least, making sure appropriate ventilation in the welding environment to eliminate any kind of potential sources of contamination is crucial for achieving porosity-free welds. By carrying out these methods, welders can properly lessen porosity and produce premium welded joints.
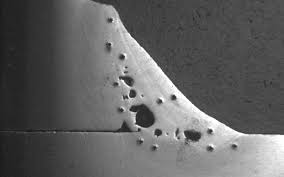
Advanced Solutions for Porosity Control
Carrying out sophisticated modern technologies and innovative techniques plays a crucial duty in accomplishing premium control over porosity in welding procedures. In addition, employing advanced welding methods such as pulsed MIG welding or customized environment welding can see here also aid mitigate porosity concerns.
One more innovative solution involves the use of sophisticated welding devices. As an example, making use of devices with integrated attributes like waveform control and sophisticated source of power can improve weld top quality and decrease porosity dangers. The application of automated welding systems with specific control over parameters can substantially decrease porosity defects.
In addition, incorporating innovative surveillance and examination innovations such as real-time X-ray imaging or automated ultrasonic testing can assist in discovering porosity early in the welding process, permitting prompt restorative activities. Overall, integrating these advanced options can significantly boost porosity control and boost the overall high quality of bonded components.
Verdict
In conclusion, recognizing the scientific research behind porosity in welding is necessary for welders and producers to produce high-grade welds - What is Porosity. Advanced solutions for porosity control can better enhance the welding process and make certain a solid and dependable weld.